What is PCB Rework?
PCB rework refers to the process of correcting defects or making modifications to a PCB after it has been manufactured. Reworking can involve a wide range of techniques, from replacing faulty components to repairing broken traces or the thin copper lines connecting components on the board. By addressing these issues, rework plays a vital role in several key areas, such as cost savings, enhanced quality, and expedited innovation.
Cost Savings
Manufacturing PCBs is a significant investment. Discarding a flawed board due to a minor imperfection can be wasteful and financially inefficient. Rework allows manufacturers to use these imperfect boards, reducing production costs.
Enhanced Quality
A misplaced solder joint or a single faulty component can impact the PCB’s functionalities. PCB rework ensures that these imperfections are identified and corrected, ultimately leading to a more reliable and higher-quality finished product.
Expedited Innovation
The field of electronics is constantly evolving. New components and design improvements are regularly introduced. PCB rework allows engineers to quickly modify existing boards to incorporate these advancements, accelerating the development cycle and bringing innovative products to market faster.
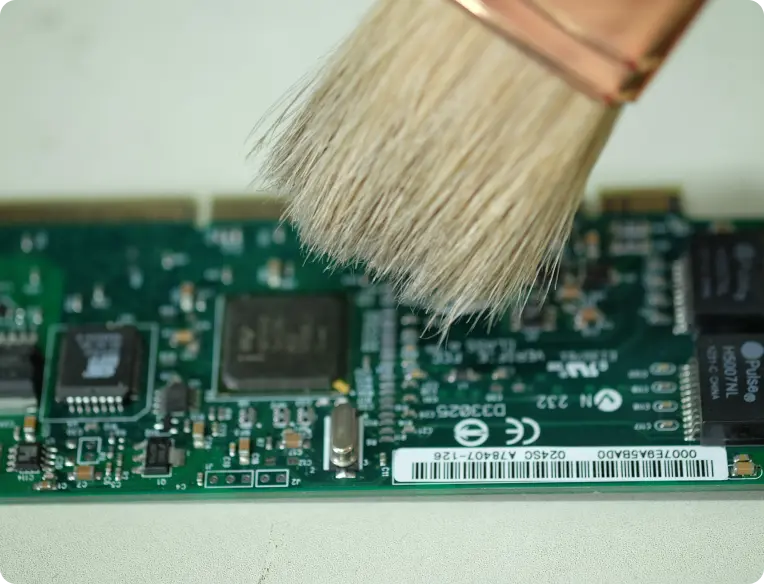
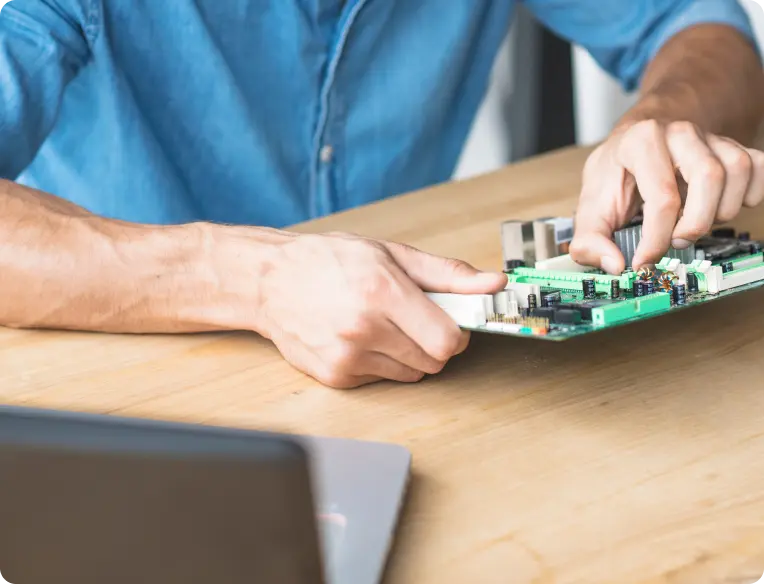
What are the Common Reasons for PCB Rework?
Even the most sophisticated PCBs can sometimes require rework. Several factors can necessitate PCB rework and impact the need to repair or replace faulty components in PCBs. Here are some of the most common reasons for PCB rework:
Soldering Defects
Soldering creates the connection between components and the PCB’s copper traces. Improper soldering can lead to various issues, such as weak connections, shorts (unintended electrical connections), and opens (broken connections). These imperfections can result in weak connections, stress on the PCB, fractures, and electrical malfunctions. Rework techniques can address these problems and ensure optimal electrical conductivity.
Component Issues
Even the most rigorously tested components can malfunction. PCB rework allows for removing and replacing faulty components, restoring the board’s functionality.
Design Errors and Defects
“>While thorough design reviews are conducted, unexpected issues can occasionally arise. These issues can be electrical, such as shorts or opens, or physical, such as misaligned components or misplaced drill holes. Design flaws, such as incorrect component selections or underestimating thermal load, can lead to overheating or component failure. Rework enables engineers to make necessary modifications to the board’s layout or component placement.
Environmental Influences
The environment in which PCBs operate can impact their need for rework. Excessively high temperatures can weaken or crack solder joints, leading to electrical failures. Rapid temperature changes can bring on stress fractures in the PCB itself, while humidity can accelerate corrosion on metal surfaces. Proper PCB material selection and conformal coatings can help mitigate environmental influences.
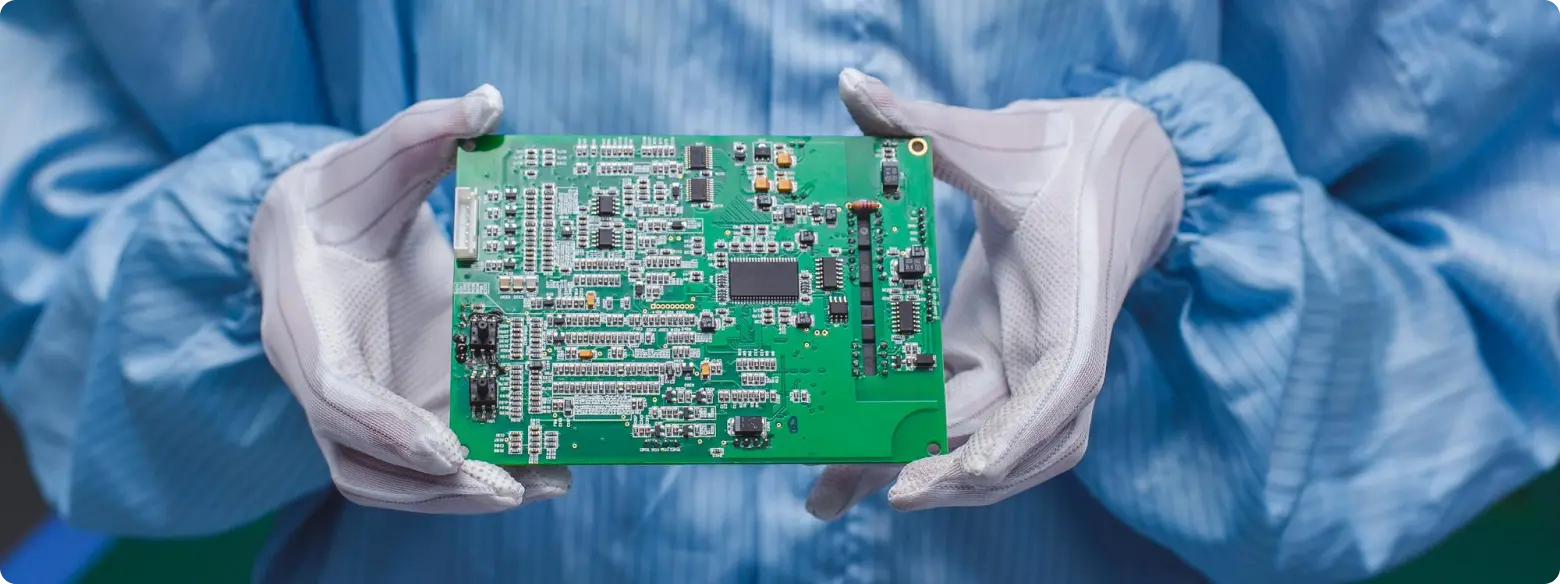
What are the Types of PCB Rework?
PCB rework typically focuses on component removal and replacement, trace and pad repair, or complex problems requiring a specialized reworking technique.
Component Removal and Replacement
The most common type of rework involves replacing faulty components. These defects can be due to soldering issues, component failure, or incorrect component selection during the design process.
The Through-Hole Technology (THT) Rework method addresses issues with components that have legs put through holes in the PCB and soldered on the opposite side. Desoldering tools are used to remove faulty components, and rework stations facilitate precise soldering of replacements.
The Surface Mount Technology (SMT) Rework technique deals with components soldered directly onto the PCB’s surface. Hot air tools or specialized rework stations melt the solder and remove the faulty component. Placement tools then ensure accurate positioning of the replacement component before reflowing the solder to create a secure connection.
Trace and Pad Repair
PCBs rely on a network of copper traces to conduct electricity. When these traces are damaged, broken, or experience shorts, the board will malfunction. When using the scratching and plating method, a scalpel is used to scratch away a small section of the damaged trace.
A layer of copper is electroplated onto the area, restoring the connection. In some cases, a jumper wire, or a thin insulated wire, is used to bridge a broken trace, creating a new electrical pathway.
Specialized Techniques
Complex problems with a PCB may require more specialized rework techniques. For example, Ball Grid Array reworking requires specialized stations that use hot air or infrared radiation to heat the BGAs precisely.
This allows for safe removal and replacement. Reballing involves removing the solder balls from a BGA and replacing them with new ones before reattaching the component to the PCB.
The Reworking Process:
Reworking a PCB involves a series of meticulous steps to correct issues discovered after the initial manufacturing process. The first step in rework is a thorough inspection, using tools like magnifying glasses, microscopes, or Automated Optical Inspection (AOI) systems to identify the problematic areas.
Once the defects are located, the next phase involves desoldering the affected components, depending on the reworking the technician needs to do. This can be achieved using a soldering iron, desoldering braid, or a hot air rework station, which precisely applies heat to melt the solder without damaging the surrounding parts.
After removing the faulty components, the PCB must be cleaned to remove residual solder and flux. The replacement components are then carefully positioned and soldered back onto the board.
During this process, maintaining the correct temperature and avoiding excessive heat is vital to prevent damage to the PCB or any new components. Finally, the reworked PCB undergoes rigorous testing, including functional tests and possibly X-ray inspections, to ensure that the rework was successful and that the board operates correctly. This detailed rework process demands precision, skill, and the right equipment.
The Importance of Skilled Technicians:
In addition to the right equipment, PCB rework demands high precision, skill, and expertise regardless of the technique. Technicians performing rework must thoroughly understand electronics principles, soldering techniques, and the intricate nature of PCBs. They must utilize specialized rework tools and adhere to strict quality control procedures.
The Future of PCB Rework:
The demand for efficient and reliable PCB rework will only increase as the electronics industry continues to miniaturize and integrate more complex components. Advancements in automation and machine vision are expected to play a more significant role in the future of rework, allowing for even greater precision. Plus, new materials and soldering techniques will be integrated into the reworking process as the technology continues to advance and evolve.
PCB rework is a crucial aspect of electronics manufacturing and repair. By mastering the techniques and understanding the necessary tools, technicians can extend the life of electronic devices, reduce waste, and save money. Although intricate, the process ensures that defects are corrected, functionality is restored, and the device’s overall reliability is enhanced.
Explore our rework options at www.elecaas.com.